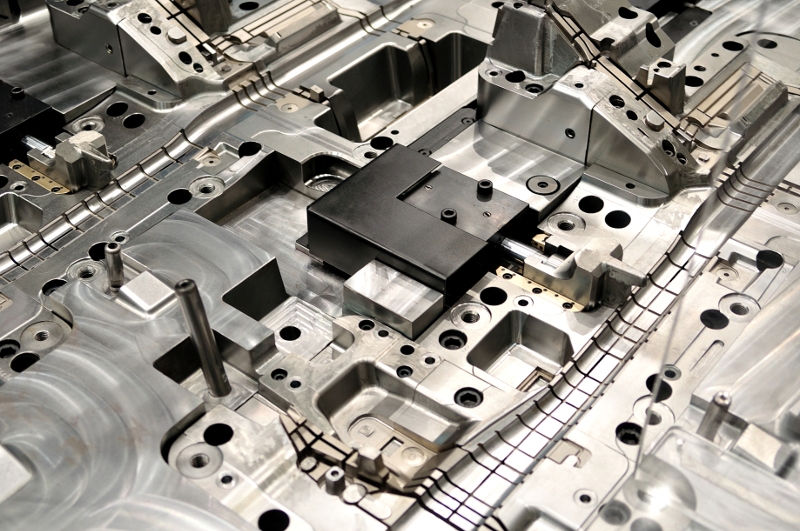
The injected plastic parts are integrated in our daily lives. Objects such as car parts, mobile phones, computers or tablets, as well as many others, are produced from injected parts.
The materials used to produce each of these moulds require specific and sometimes unique characteristics. It is, therefore, decisive the selection of the most suitable steel for each mould. The specificity of each mould also requires the specification of the steel that best suits each project. This is because the mould industry is a very demanding sector, in which steel is subjected to different types of requests.
Since the problems that usually arise are known and identified by the industry, choosing the correct steel may be the solution. The mould maker has to consider, in addition to the mould production cost, the cost of all associated maintenance such as repetitive polishing, cleaning or replacement of broken or worn parts. In addition, downtime costs, overtime, penalties for delays in deliveries and loss of customers must also be considered. In the end, it is still important to maximize mould durability and productivity.
The goal is to achieve the lowest possible cost per piece produced. Overall, the value of steel represents only about 5 to 10% of the cost of the tool. Its value in the overall cost (manufacturing + lifetime) will be even less significant. In this way, the choice of the correct tool steel is critical.